Inwestor ma prawo wymagać, aby np. przez okna wpadało dużo światła do domu, biura czy szpitala. Projektując lub wznosząc obiekt o niskim zapotrzebowaniu na energię, nie możemy więc być niewolnikami grubości izolacji czy ograniczeń technologicznych popularnych rozwiązań oferowanych na rynku.Wprzypadku fasad możemy wybrać np. tradycyjną ścianę trójwarstwową, ścianę dwuwarstwową z izolacją ETICS, fasadę wentylowaną. Każde z tych rozwiązań niesie ograniczenia, które czasami zmuszają do rezygnacji z doskonałej izolacji cieplnej przegrody.
W przypadku ściany trójwarstwowej najczęściej walory estetyczne fasady biorą górę nad efektywnością cieplną. Ten rodzaj muru jest jednym z najdroższych rozwiązań i jednocześnie jednym z najbardziej prestiżowych. Z założenia brak jest możliwości ingerencji w izolację przez wiele lat. Jest ona bowiem ukryta pomiędzy murem konstrukcyjnym a ścianą osłonową. Ściana składa się z części konstrukcyjnej (grubości np. 19 cm) oraz np. 12 cm klinkierowego muru osłonowego z izolacją w postaci standardowej wełny mineralnej (λD = 0,042 W/mK). Aby dla takiej ściany uzyskać przyzwoity współczynnik przenikania ciepła U = 0,21 W/m2K, musi ona mieć całkowitą grubość min. 51 cm. Ta sama ściana z wykorzystaniem ISOVER MULTIMAX 30 uzyska podobne parametry przy całkowitej grubości 46 cm.
Zaoszczędzone 5 cm grubości przegrody zewnętrznej w przypadku budynku parterowego o wymiarach zewnętrznych 17 x 10 m to m.in.:
● dodatkowa powierzchnia (ok. 2,5 m2);
● oszczędność min. 4 m3 betonu pod mniejsze fundamenty;
● łączne korzyści finansowe – kilkanaście tysięcy złotych;
● dodatkowe doświetlenie dzięki mniejszej grubości ściany przy tej samej wielkości okien;
● uzyskanie parametrów cieplnych ściany zewnętrznej 3-warstwowej konkurencyjnych wobec ścian dwuwarstwowych podobnej grubości.
Więcej na temat skutecznego izolowania fasad wełną Isover >>
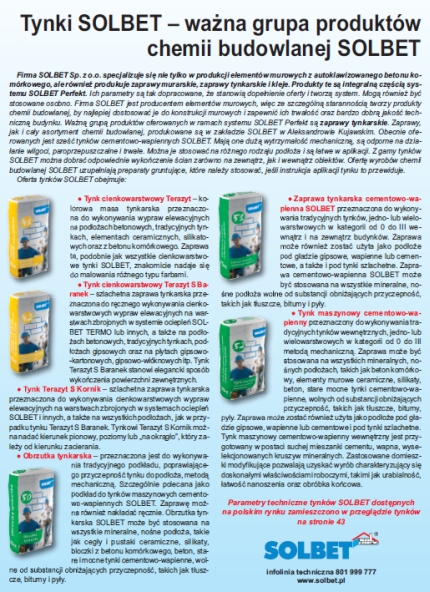
prof. dr hab. inż. Józef Jasiczak, Politechnika Poznańska
Betony o charakterze architektoniczno-dekoracyjnym na stałe weszły do praktyki budowlanej. Znalazły zastosowanie przy realizacji budynków o reprezentacyjnym charakterze, jak np. Centrum Nauki Kopernik i budynek administracyjny Kancelarii Sejmu RP w Warszawie, Muzeum Lotnictwa Polskiego w Krakowie czy Muzeum ICHOT w Poznaniu.
Po architektoniczny beton elewacyjny sięgają najwięksi obecnie architekci na świecie, począwszy od Zahy Hadid (Muzeum Maxxi w Rzymie) po Santiago Calatravę (Auditorio na Teneryfie, Muzeum Sztuki w Milwaukee, Port Lotniczy w Bilbao) czy trio architektoniczne Fernando Martin Menis, Felipe Artengo Rufino, José Maria Rodriguez Pastrana (autorzy projektu wymienionego Centrum Kongresowego MAGMA). Wszystkie budowle powstały po 2005 r. i są wizytówką zastosowania betonu początku XXI wieku.
W artykule ponadto: wymagania dotyczące betonu architektonicznego oraz problemy technologiczne występujące podczas wykonywania ścian z betonu architektonicznego
LED-y wygrywają z powszechnie stosowaną techniką w iluminacji obiektów i można je stosować w miejscach, w których użycie konwencjonalnych źródeł światła do tej pory nie było możliwe. Niezwykła jakość światła, możliwość tworzenia form o dowolnych rozmiarach i kształtach, a także różnym natężeniu i barwach sprawiają, że jest to idealne narzędzie do podkreślania zarówno fasad obiektów, jak i ich architektonicznych detali. Produkty LED umożliwiają także przemianę statycznej bryły budynku w multimedialny ekran.
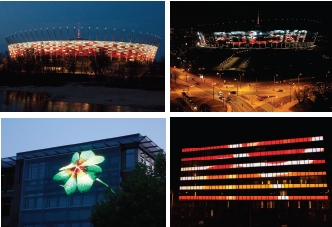
Zalety oświetlenia LED należą m.in.:
● najwyższa ze wszystkich dotychczas oferowanych źródeł światła trwałość, którą szacuje się co najmniej na 40 – 50 tys. godzin (powszechnie stosowany asortyment oświetleniowy 1 – 15 tys. godzin);
● bardzo dobra jakość oświetlenia LED (wierność do 90%), czyli generowane jest światło porównywalne do światła z najlepszej jakości świetlówek;
● diody elektroluminescencyjne są niezwykle ekonomiczne;
● wytrzymałość i duża skuteczność świetlna;
● bezpieczeństwo użytkowania (nie wytwarzają promieniowania nadfioletowego UV i podczerwonego IR).
Więcej informacji na temat oświetlenia LED marki OSRAM >>
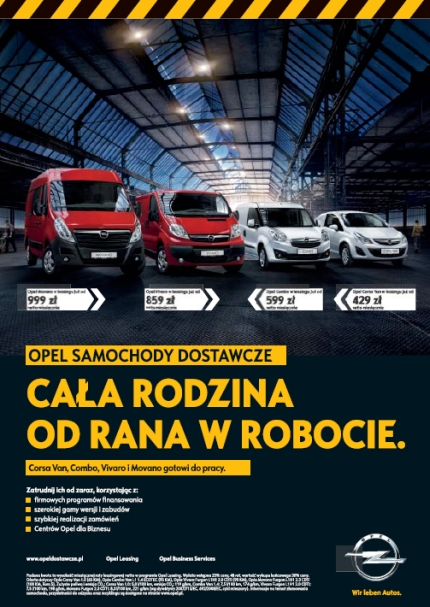
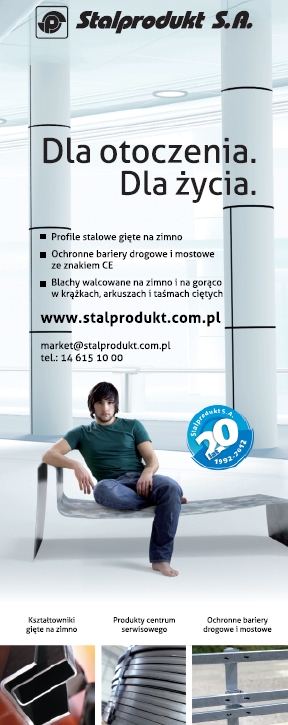
dr inż. Józef Adamowski, Politechnika Wrocławska
Inżynieria fasad (z angielskiego Facade Engineering) to zakres prac inżynierów fasad obejmujący zarówno projektowanie nowych budynków wykonanych z najnowocześniejszych materiałów i przy wykorzystaniu najnowszych technologii, jak i podniesienie standardu funkcjonowania istniejących obiektów biurowych oraz modernizacja budynków zabytkowych z zachowaniem ich dotychczasowego wyglądu.
Inżynierię fasad wprowadzili specjaliści z firmy Arup Facade Engineering, a w Polsce tę nową dziedzinę wiedzy zainaugurował w 2011 r. dr hab. Tomasz Błaszczyński z Politechniki Poznańskiej.
Inżynieria fasad wymaga ścisłej współpracy architektów inżynierów, geologów, metalurgów, kosztorysantów, projektantów, fizyków budowli. Współpraca ekspertów jest ważną częścią podejmowania spójnych decyzji, a różnorodne umiejętności są nierozdzielnie związane z projektowaniem. Przykładem może być opracowywanie powłoki nowego magazynu dla firmy Selfridges w Birmingham w Wielkiej Brytanii (2003; autorzy: Future Systems; konstrukcja: Arup Façade Engineering), składającej się z okrągłych, trójwymiarowych, zakrzywionych, metalowych dysków. W projekcie tym należało wziąć pod uwagę wiele aspektów, poczynając od typu materiału, którego można byłoby użyć, aby uzyskać odpowiedni kształt, przez produkcję, kończąc na sposobie montażu kręgów i uniemożliwieniu wspinania się po budynku.
Wiele przykładów kształtowania fasad wynika z założeń środowiskowych, np. wymagania dotyczące magazynowania energii, zgodnie z założeniem przyjętym przez architekta, wymuszają zastosowanie okładziny szklanej o odpowiednich parametrach i wymiarach. W celu zredukowania strat energii, szkło użyte do wykonania fasady jest specjalnie powlekane. Można także zastosować fasadę podwójnie szkloną. Obydwie opcje są bardziej ekonomiczne niż zastosowanie na zewnątrz – w celu polepszenia izolacyjności obiektu – dużej liczby paneli z kamienia, płytek ceramicznych czy metalu.
Fasadę budynku biurowego Metropolitan w Warszawie (2003; autorzy: Foster & Partners we współpracy z pracownią JEMS Architekci; konstrukcja: Arup Façade Engineering) zaprojektowano z 1250 żeberek z litego granitu, mocowanych do ściany osłonowej budynku, które pełnią funkcję żaluzji. Wiele trudności w procesie produkcji, podczas transportu, wznoszenia i montażu spowodowała masa materiału – każda żaluzja waży 550 kg, dlatego też przeprowadzono szczegółową analizę bezpieczeństwa projektowanych wsporników. Rozwiązaniem był system, który pozwalał na montaż granitu do wsporników poza placem budowy, a następnie na zawieszenie wykonanych prefabrykatów. Ostatecznie przez cztery otwory wywiercone w kamiennych płytach przeprowadzono stalowe pręty i zamocowano do profilu stalowego w kształcie litery L.
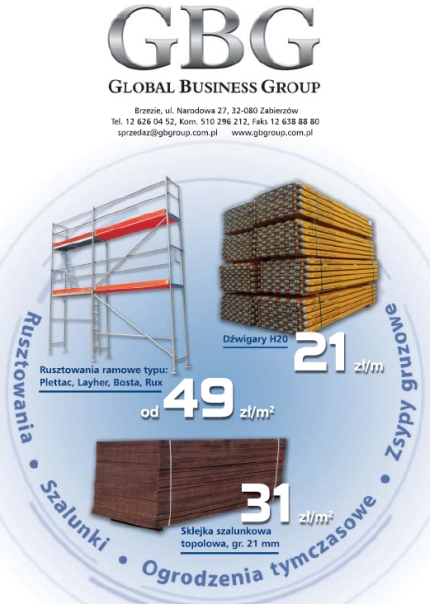